TWO BLACK OXIDATION PROCESSES AT A GLANCE
We use two different black oxidation processes in our surface treatment plants. We distinguish between technical and optical black oxidation. While optical black oxidation produces a black oxide conversion layer by immersion in hot salt solutions, technical black oxidation fulfils functional requirements in addition to the uniform black surface. Further information can be found in the following descriptions of the respective processes. If you have any questions, please contact our experts, who will be happy to advise you.
![[Translate to English:] Technisches Brünieren Brünierte Lagerringe](/fileadmin/_processed_/5/7/csm_mittlerer-lagerring-bruenieren-01-m_540ab5d378.jpg)
Tribological properties of a black oxidation coating
- Improved run-in behaviour of bearing components
- Reduction of slippage damage through better resistance against smearing
- Improved properties in event of inadequate lubrication, this avoids the risk of cold welding and various other serious surface damages – increased operational safety and reliability
- Improved adhesion of lubricant oil or grease
- Reduced effects of aggressive oil components on the bearing steel
- Lower risk of fretting corrosion
- Lower hydrogen permeation in the bearing steel
- Improved resistance against surface-induced damage
- Improved frictional properties in event of inadequate lubrication.
Advantages due to tribological properties of a black oxidation coating
- Improved run-in behaviour of bearing components, a basis for subsequent error-free operation.
- Longer component service life due to black oxidation.
- Increased resistance to harmful environmental influences that may occur.
- For steel-to-steel contacts due to brief breakdown of the lubricating film: Avoids the risk of cold welding and various other serious surface damages. Results in increased operational safety.
Cost savings and operational safety improvement due to longer service life of the bearings and bearing components.
Process properties
AIM: Functional requirements and uniform black surface
TECHNOLOGICAL REQUIREMENTS: Plant with extraction system and exhaust air scrubber required
ENERGY REQUIREMENTS: Determined based on the boiling properties of black oxidation baths, heat output calculations for steel warming => much greater heating output required
WORKING PROCESS: Based on specific experience values regarding sequences and time, very detailed final inspection. Colour and no stains must also be guaranteed.
Detailed, multiple and frequent inspection intervals for process stability of all process baths.
TYPE OF FINAL INSPECTION: Wipe test/abrasion resistance, acetic acid test, copper sulphate test, coating weight, REM inspections, EDX, XRD, etc., special tests dependent on bearing type
CONSERVATION: Functional properties of conservation oils must
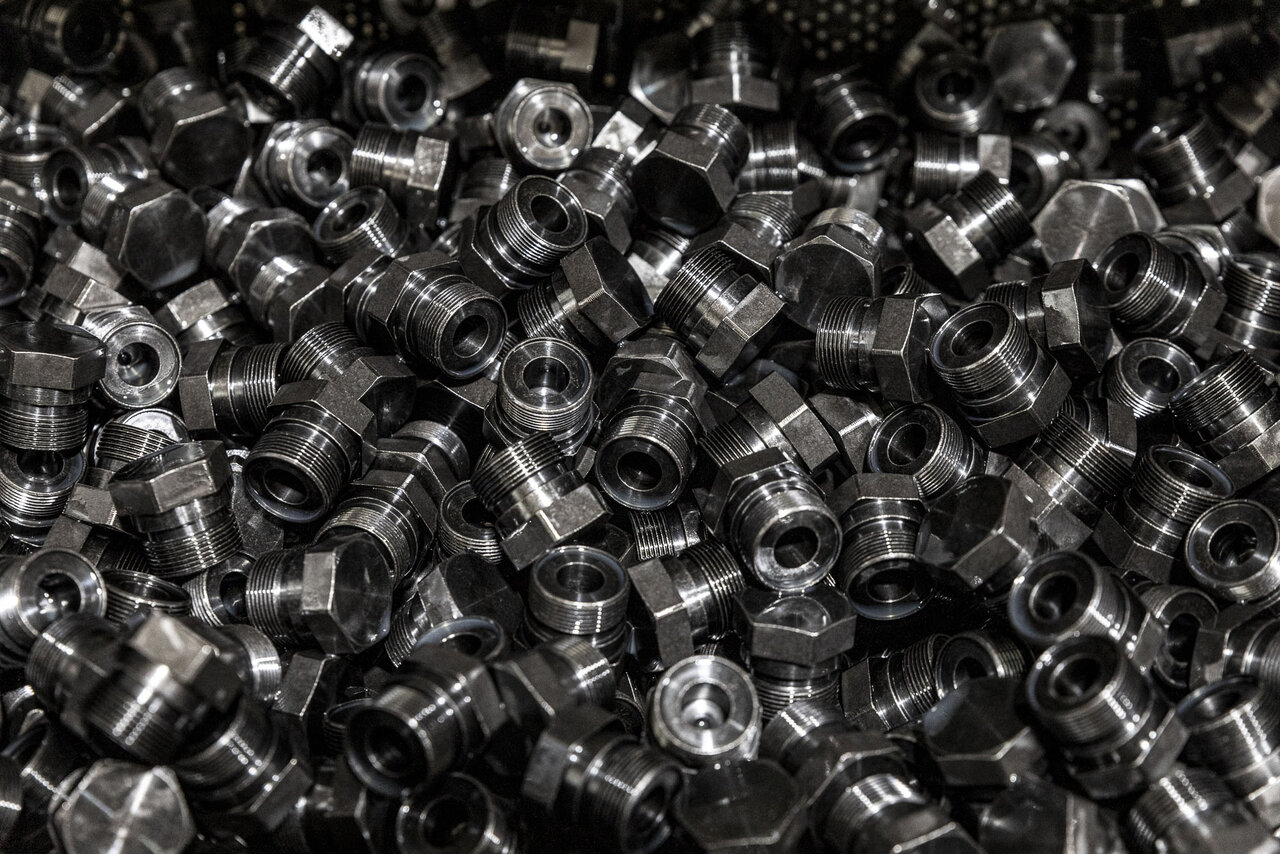
State of the art black oxidation: DIN 50938 2018:01
Thermally generated black oxidic conversion coating, produced by dipping in hot salt solutions.
Application area: This standard sets out the requirements and test methods for black oxide coatings on ferrous metal components generated by a chemical reaction in an immersion process. Black precipitation generated at room temperature using acidic, heavy metal-containing solutions and other processes for generating black oxidation coatings do not form part of this standard.
Characteristics of a black oxidation coating
Composition | Iron (II,III) oxide = Fe3O4= magnetite or ferrous-ferric oxide |
Coating colour | black |
Layer thickness | 0,5 - 2,0 µm (1 µm ≈ 5 g/m2) |
Surface density | 4,5 - 10 g/m2 usually method B |
Surface structure | Maintained, no fitting problems |
Other coating properties | Smooth and unstructured Resistant to bending and abrasion Magnetic properties of the base material are maintained Electrical conductivity of base material is maintained to the greatest possible extent |
Process properties
AIM: Optically black surface, usually without functional requirements
TECHNOLOGICAL REQUIREMENTS: Plant with extraction system and exhaust air scrubber required
ENERGY REQUIREMENTS: Determined for main baths via heating time of bath volumes
WORKING PROCESS: based on classic experience values regarding sequences and time, no detailed final inspection. Only colour, wear and staining are checked.
Normal inspection intervals for process stability of all process baths
TYPE OF FINAL INSPECTION: Wipe test/abrasion resistance, acetic acid test, copper sulphate test
CONSERVATION: Usually only based on corrosion protection